New solution for thermal power plant start-up optimization
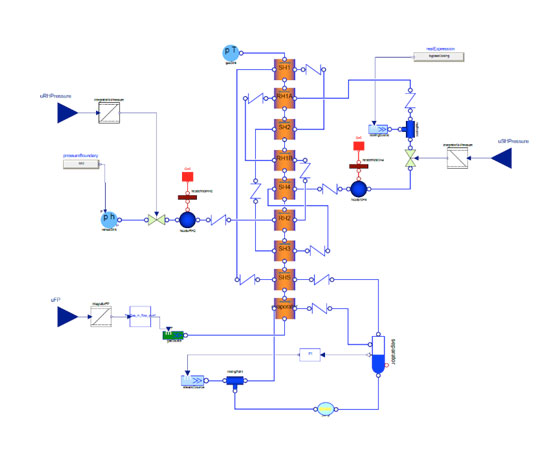
Increased flexibility for power plants energy production
During the spring and summer of 2015, a collaboration between Modelon, Vattenfall and Lund University resulted in a development of a new solution for start-up optimization of a thermal power plant [1].
The collaboration took place within the MODRIO project and was a continuation work with Vattenfall concerning optimization of Vattenfall’s thermal power plant Jänschwalde in Germany.
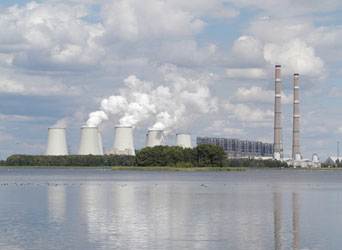
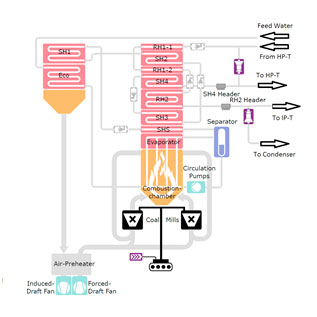
Why start-up optimization
As intermittent power production such as solar and wind power is increasing, the required flexibility of thermal power plants is also increasing. It is expected that the thermal power plants will experience more startups and stops, depending on electricity price and intermittent power production.
Today’s power plants are not designed for such frequent start-ups, and the thermal stress in certain components resulting from starts can be problematic. If the thermal stress is too high, the life-span of the plant is reduced.
Achieve a robust computation & optimization
One way to reduce the impact is to perform model-based optimized starts, which also could reduce the fuel consumption and environmental impact. This methodology requires a good model of the plant as well as a framework that can perform computations and optimizations. The main objectives of this collaboration were to create such a framework consisting of:
- A state estimator for the plant, that is an algorithm that updates the states of a plant model based on plant measurements.
- A non-linear model prediction controller (NMPC) that can, based on the result of the state estimator, optimize the control signals of the plant, to drive it towards a predefined operating condition while minimizing fuel costs and not violating thermal stress constraints.
Steam cycle model
As a starting point, the team had a very detailed Modelica model of a steam cycle in the plant from a collaboration between Vattenfall and Rostock University [5] and a simplified but uncalibrated model derived in [3], suitable for optimization. Both models were developed using Dymola.
Additionally, a Python class in JModelica.org for NMPC, based on a Modelica model implemented in [2] was available. The control loop was to be used on the detailed Modelica model as a substitute for the real plant, see Figure 3.
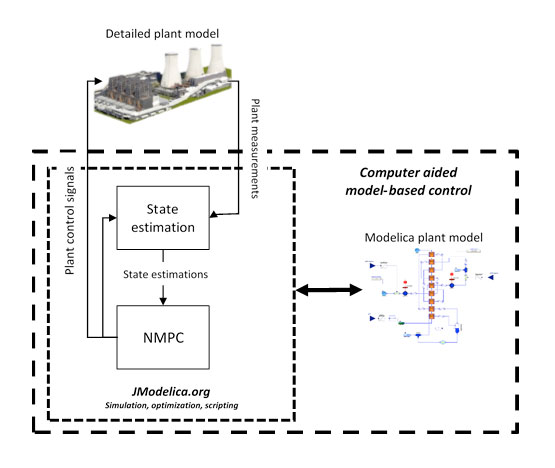
Soft start-up
There are several types of start-ups of a thermal power plant depending on how long the plant has been at stand still. In discussion with Vattenfall, it was decided that a soft-startup used when the plant has been shut down for 12-48 hours should be considered.
It was also decided that the focus would be on the initial phase of the start-up when oil burners are used to quickly start the combustion process, as this phase is the most costly part of the startup and hence when gains of optimization would potentially be greatest.
Simplified steam cycle model
Both the state estimator and the NMPC used the simplified model where, compared to the detailed model, unused parts been removed and some highly detailed parts simplified. The dynamics in the simplified model focus on the components that are important at start-up. These components are the steam side and walls of heat exchangers and walls of headers and separators, where the thermal stress must be limited via control to not reduce plant life span.
The parameters of the simplified model, specifically the heat transfer coefficients in the heat exchangers and the pipe flow coefficients, were estimated to fit the detailed model during a reference soft start-up.
The simplified Modelica model of the steam cycle studied is seen in Figure 4.
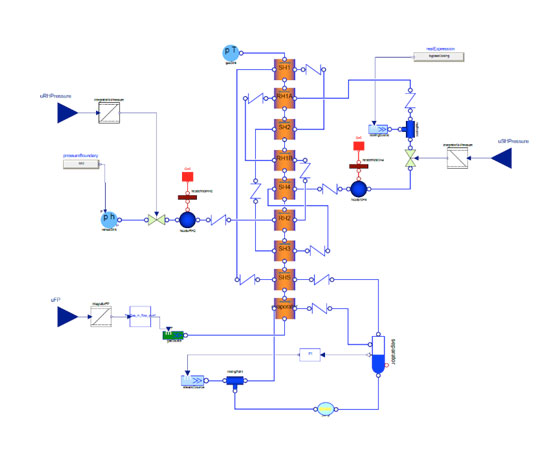
For state estimation of the thermal power plant, an unscented Kalman filter (UKF) was implemented by the team as a Python class. This class contains high-level functions to create an UKF from a generic Modelica model, perform predictions based on inputs and known states, and perform corrections based on measurements. The team ensured that the UKF were able to handle both model errors, by introducing disturbance states, as well as noise on all measured signals.
The available NMPC class in JModelica.org was used throughout the collaboration. A quadratic cost function, penalizing deviations from desired operating condition of firing power, live steam temperature and pressure, and reheater steam pressure, was used in the control loop.
Constraints on the thermal stress were set using soft constraints, meaning that the thermal stress can exceed the constraints but at a high cost in the optimization. Soft constraints are mainly used to prevent unfeasible optimization problems for the NMPC loop.
Tests
The team ran several types of tests to analyze the impact of different weights in the cost function on the optimal solution, as well as different types of model errors.
Figures 5 – 7 below show the results from a test with mismatch in the heat transfer coefficient of the evaporator, as well as disturbances acting on both boiler fire power and reheater by-pass valve.
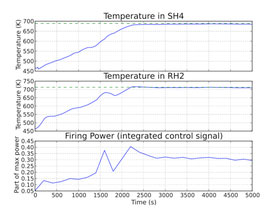
Despite these complications, the solution framework is able to drive the temperature and pressure in superheaters and reheater to desired values, as can be seen in the top graphs in Figures 5 and 6, using the firing power and by pass valve, shown in lower graphs in these two figures.
The thermal stress constraints shown in Figure 7 only have minor violations deemed acceptable from Vattenfall’s point of view.
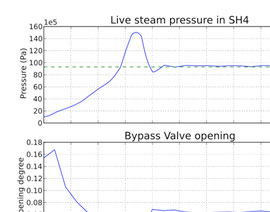
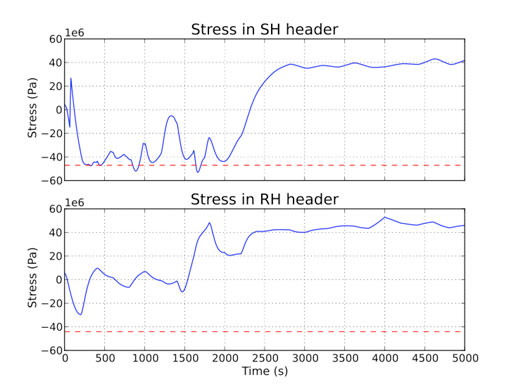
Save costs & environment
The analysis of several start-up optimizations showed that the considered phase of the soft startup could be accomplished in around 40 minutes, a saving of about 70 minutes compared to a reference start-up.
Savings of up to 60% of firing power could also be made by using the model-based solution. With the thermal stress ensured within limits during the major part of the start-up, the life span of the thermal power plant would not be decreased significantly.
More info
The plant models were developed using Dymola from Dassault Systèmes and Thermal Power Library from Modelon.
JModelica.org, a Modelica-based platform for optimization, simulation, and analysis of complex dynamic systems, provides the optimization framework for this work. In addition to the NMPC used in this project, JModelica.org also includes dynamic optimization, optimization-based state estimation, and parameter estimation method.
OPTIMICA Compiler Toolkit is an extension of JModelica.org, which also includes enhanced solvers and support for steady-state simulation and optimization. A tutorial for OPTIMICA Compiler Toolkit centered around the power plant start-up optimization is available at demand.
If you want to know more about these solutions, don’t hesitate to contact us!
References
[1] Andrén, M. and C. Wedding (2015). Development of a solution for Start-up Optimization of a Thermal Power Plant. MSc Thesis ISSN: 0280-5316. Dept. of Automatic Control, Lund University, Lund, Sweden.
[2] Axelsson, M. (2015). Nonlinear Model Predictive Control in JModelica.org. MSc Thesis ISSN: 0280-5316. Dept. of Automatic Control, Lund University, Lund, Sweden.
[3] Runvik, H. (2014). Modeling and start-up optimization of a coal-fired power plant. MSc Thesis ISSN: 0280-5316. Dept. of Automatic Control, Lund University, Lund, Sweden.
[4] Julier, S. and J. Uhlmann, (2004), Unscented Filtering and Nonlinear estimation, Proceedings of the IEEE 92, pp 401-422.
[5] Hubel, M., et al., Modelling a Lignite Power Plant in Modelica to Evaluate the Effects of Dynamic Operation and Offering Grid Services, Proceedings of the 10th International Modelica Conference, March 10-12, 2014, Lund, Sweden, pp. 1037-1046.